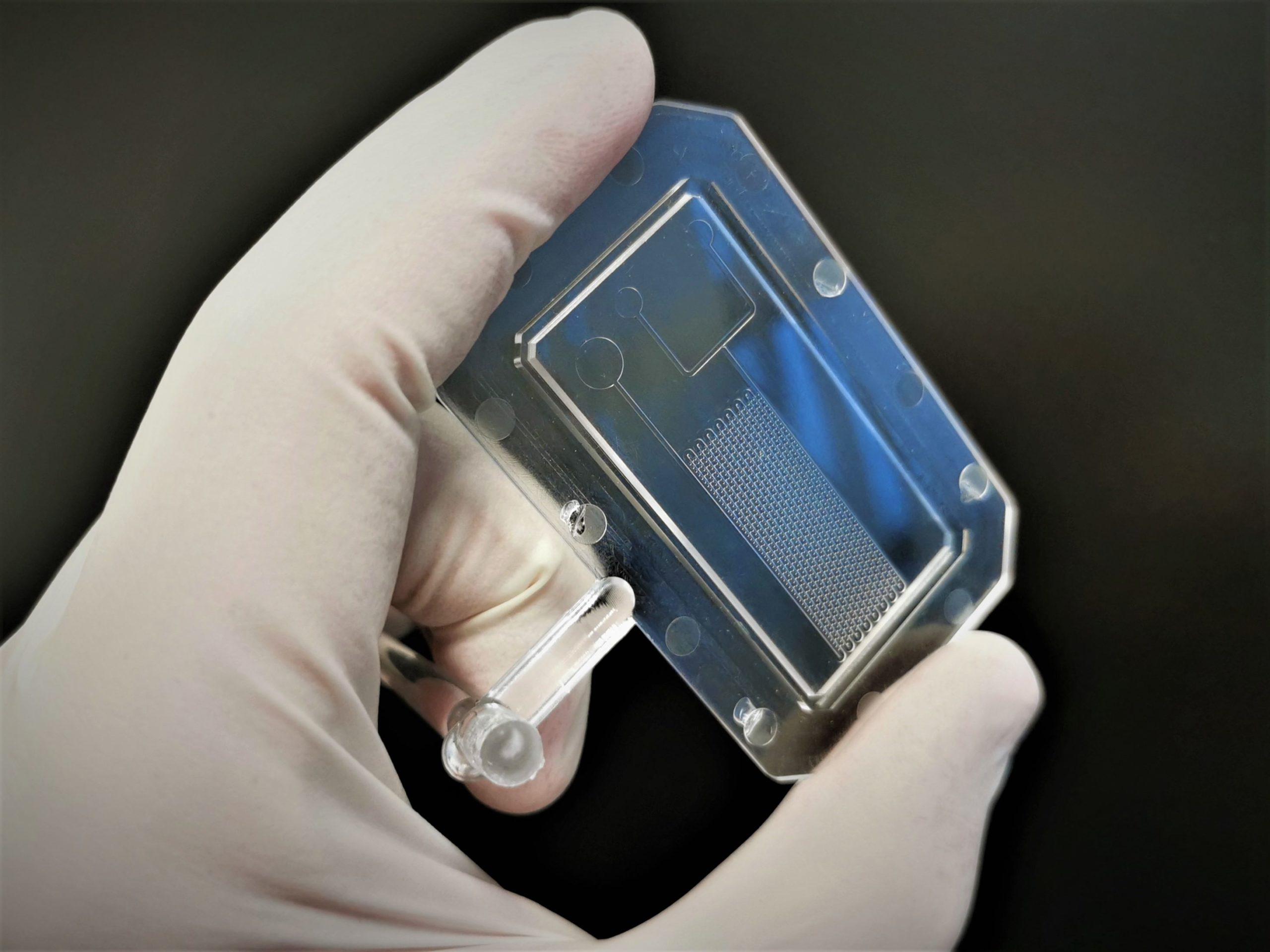
Reducing Lead Times in Precision Micro Molding for Microfluidics
Production of micro-structured injection moulds of micrometric precision and optical quality.
Replication of microfluidic parts, with appropriate thermoplastic material, in industrial conditions.

Custom Microfluidic Solutions
World-class technologies supported by high precision metrology

Mold Making
State of the art micromachining facilities, incl. 3D-micro-EDM-milling technique (Sarix SX100HPM)
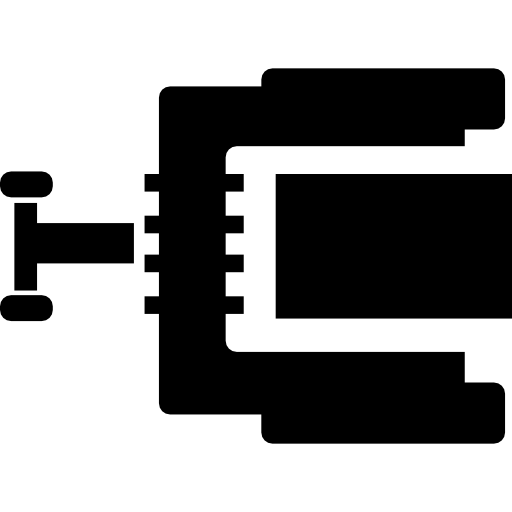
Injection Molding
Injection-compression press (FANUC roboshot S100iA 330), including advanced thermoregulation technology.
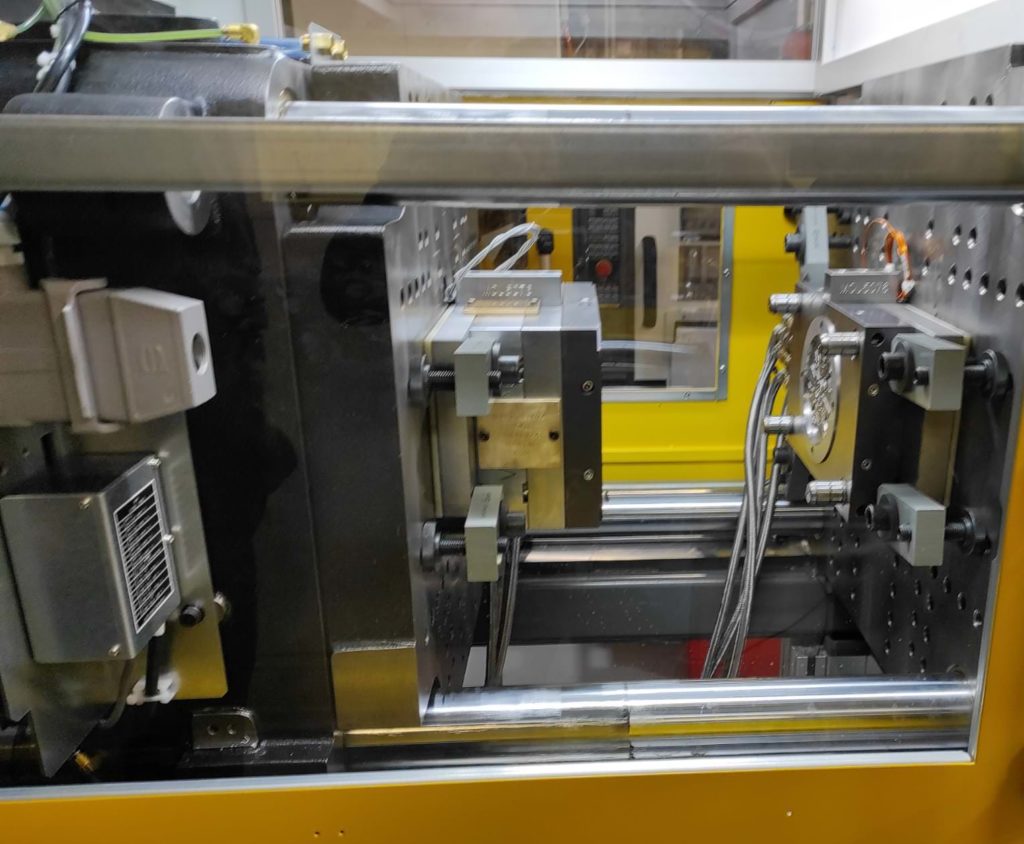
Expertise
Our multidisciplinary platform offers support for the realization of prototypes and larger series of microfluidic devices by precision micro-molding, at reduced cost, and with lead times that can be up to 3 times shorter than a traditional approach. Prototypes can already include complex geometries and specific surfaces.
From small series and prototypes to industrial mass production
This platform is available to any company, University or Research Center willing to develop new microfluidic devices by precision micro-molding in an optimal time.
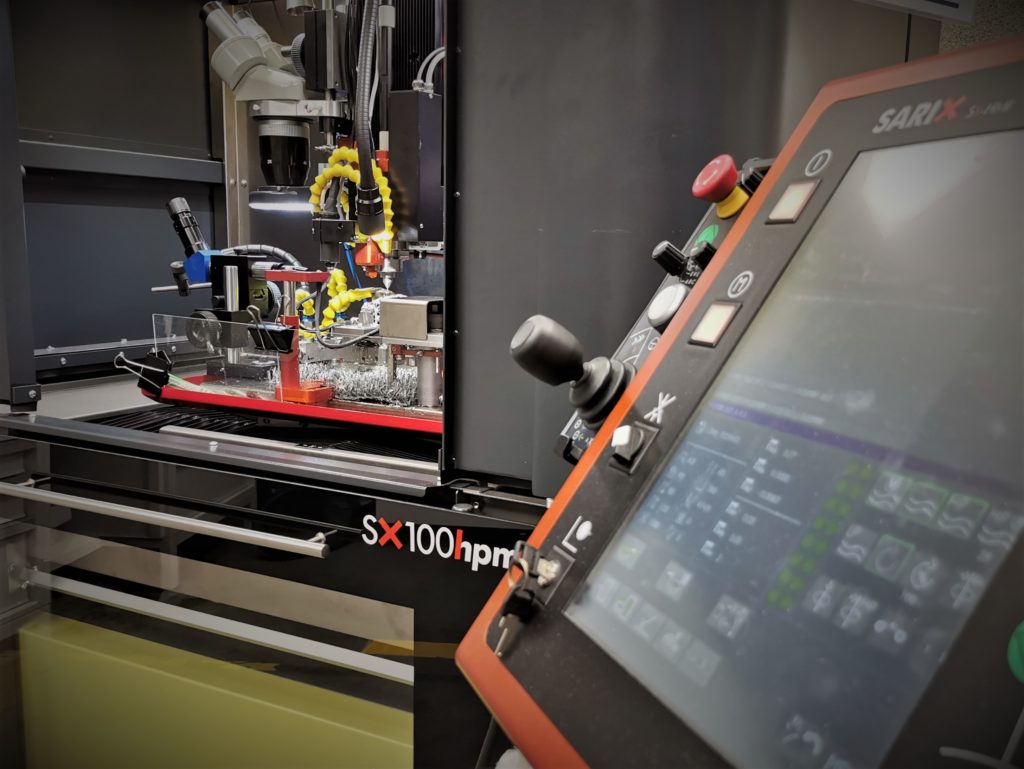
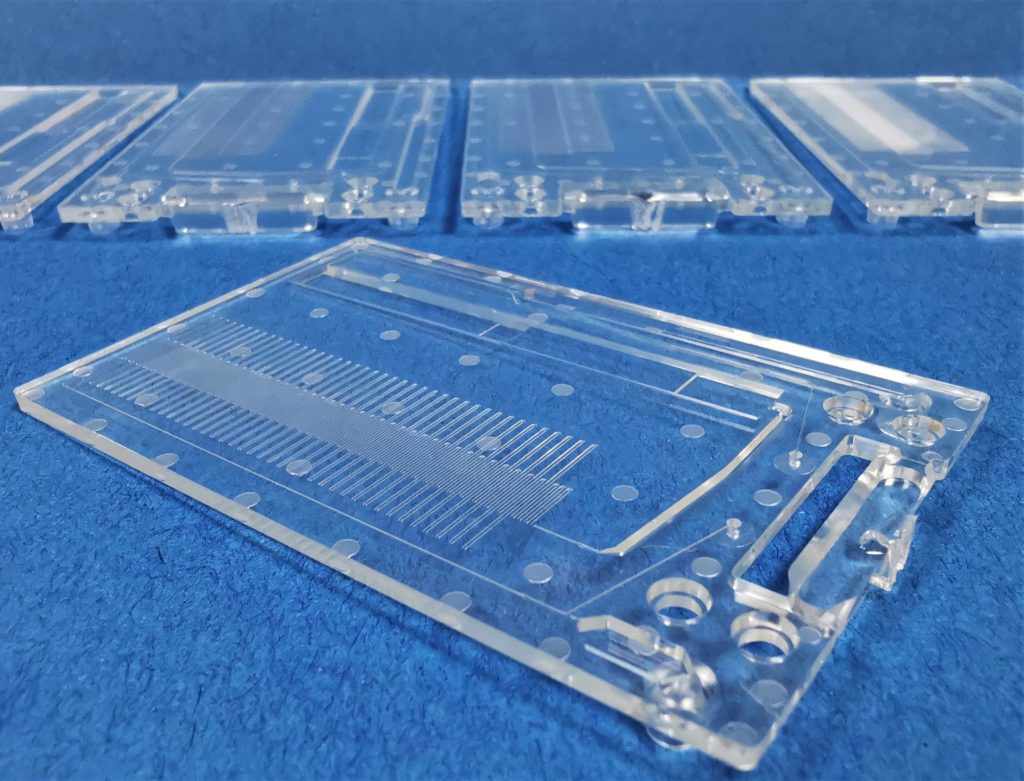
Various Fields Of Application
Diagnostics
Life Science Research
Drug delivery
Pharmaceutical research
Analytical devices for environment
Food control
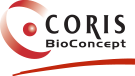
During the implementation of the microfluidic platform at Coris BioConcept, development of applications was hampered by the lack of flexibility in the realization of microfluidic chips and by the delays in obtaining the injected parts to be evaluated.
The precision-micro-molding platform allows to considerably reduce the waiting time between the prototypes and the manufacturing of injection inserts, and obtaining injected parts thanks to the proximity between end-users, developers and producers.
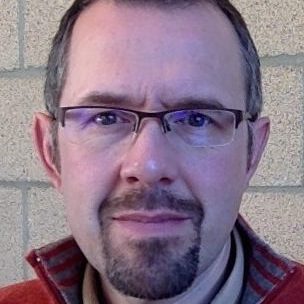
Pascal Mertens – Coris BioConcept
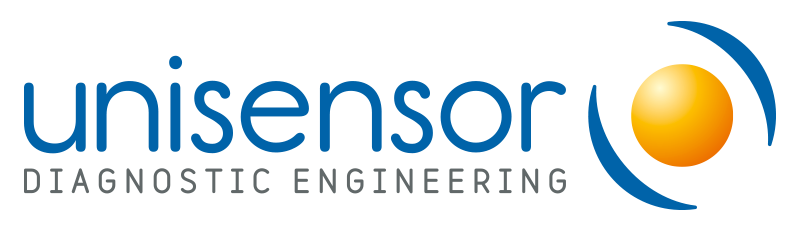
Developing a capillary-driven microfluidic cartridge, we spent 2 years optimizing our cartridge with a fast prototyping technique which at the end was not transposable to high mass manufacturing due to injection constraints and surface properties.
To get our final injected product, we had to restart the development using injection molding. We needed 6 other iterations and spend 18 additional months before reaching our target. If this platform would have existed before, we would have reached the market 1 year earlier.
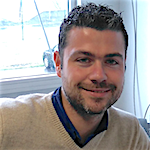
Noan Nivarlet – Unisensor